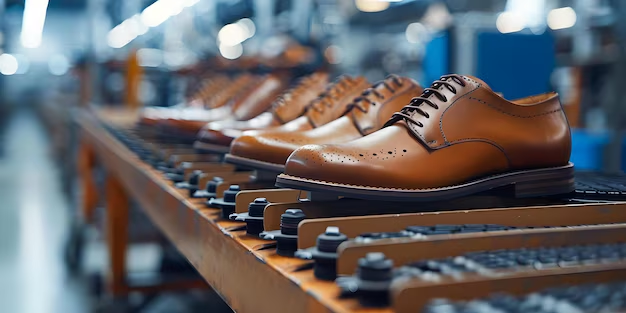
Resumen Ejecutivo
Este caso de estudio documenta cómo AICEN transformó la producción de una de las principales fábricas de calzado en León, Guanajuato, mediante la implementación de compresores KAESER. El proyecto resultó en una mejora del 40% en eficiencia energética y un aumento significativo en la calidad de producción.
El Cliente
- Industria: Fabricación de Calzado
- Ubicación: León, Guanajuato
- Capacidad: 5,000 pares diarios
- Operación: 2 turnos, 6 días por semana
- Aplicaciones de aire comprimido:
- Máquinas de costura neumática
- Prensas para suelas
- Pistolas de pegamento
- Sistemas de corte automatizado
- Máquinas de conformado
📱 ¡Contáctenos Hoy!
- Llame al: (477) 714 20 42
- Correo: ventas@airequipos.com.mx
Situación Inicial
La fábrica enfrentaba diversos retos:
- Sistema antiguo con múltiples compresores pequeños dispersos
- Presión irregular que afectaba la calidad del pegado
- Alto consumo energético
- Frecuentes paros en líneas de producción
- Contaminación del aire que afectaba el acabado del calzado
Diagnóstico AICEN
Se realizó un análisis completo durante 2 semanas:
- Medición de consumo real: 250 CFM promedio
- Picos de demanda: 320 CFM
- Caídas de presión significativas
- Fugas detectadas: 25% del aire producido
- Calidad del aire inadecuada para procesos de acabado
Solución KAESER Implementada
Equipo Principal
- 1 × Compresor KAESER SK 25T
- Potencia: 25 kW
- Control de velocidad variable
- SIGMA PROFILE integrado
- 1 × Compresor KAESER ASK 35
- Potencia: 22 kW
- Respaldo y gestión de picos
- Sistema de Tratamiento de Aire
- Secador refrigerativo TD 76
- Filtros coalescentes
- Separador de condensados ECO-DRAIN
- SIGMA AIR MANAGER 4.0 Basic
- Control inteligente de múltiples compresores
- Monitoreo en tiempo real
- Alertas preventivas
Plan de Implementación
Fase 1: Preparación
- Diseño de nueva red de distribución
- Planificación de instalación sin afectar producción
- Preparación de área de compresores
Fase 2: Instalación
- Montaje de equipos nuevos
- Instalación de tubería nueva
- Conexión de sistemas de control
Fase 3: Optimización
- Eliminación de fugas
- Ajuste de presiones por área
- Capacitación de operadores
Resultados Alcanzados
Mejoras Cuantitativas
- 28% de reducción en consumo eléctrico
- Retorno de inversión en 15 meses
- Reducción de fugas a menos del 5%
- Presión estable a 6.5 bar
- Reducción del 60% en costos de mantenimiento
Mejoras en Producción
- Eliminación de rechazos por mal pegado
- Mejor acabado en productos finales
- Zero paros por fallas en aire comprimido
- Aumento de 15% en productividad
Beneficios Adicionales
- Aire limpio para todas las aplicaciones
- Menor ruido en área de producción
- Sistema centralizado de fácil control
- Mantenimiento preventivo programado
Programa de Servicio AICEN
- Mantenimiento programado
- Respuesta técnica en menos de 2 horas
- Análisis periódico de eficiencia
- Stock permanente de filtros y refacciones
- Capacitación continua al personal
Testimonial
«La inversión en compresores KAESER ha sido fundamental para mejorar nuestra calidad y reducir costos. El servicio de AICEN ha sido excepcional, siempre atentos a nuestras necesidades.»
– Gerente de Producción, Fábrica de Calzado
Aspectos Destacados del Proyecto
- Calidad Mejorada
- Aire más limpio para acabados perfectos
- Presión constante para pegado uniforme
- Eficiencia Energética
- Sistema adaptado a demanda real
- Tecnología de velocidad variable
- Confiabilidad
- Respaldo automático
- Mantenimiento preventivo
- Soporte Continuo
- Servicio local en León
- Respuesta rápida
🏭 ¿Su Fábrica Será la Siguiente Historia de Éxito?
AGENDE SU AUDITORÍA GRATUITA AHORA